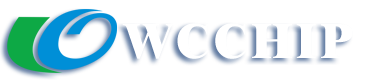
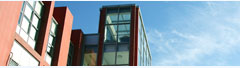
Chip Supplies
POSITIVE RESIST PR1-500A
2014-09-17 10:00:36
(2).jpg)
Description
• Positive Resist PR1-500A is a positive tone photoresist designed for 365 or 436 nmwavelength exposure, using tools such as wafer steppers, scanning projection aligners,proximity printers and contact printers. PR1-500A excels in applications when superioradhesion is required. Use of adhesion promoters, such as HMDS is not recommendedwith PR1-500A.
• These are the advantages of PR1-500A over other resists:- superior resolution capability- fast photospeed- superior linewidth control due to suppression of reflective notching- substrate adhesion which is superior to that of any commercial positive resist- ease of removal after RIE process- shelf life exceeding 1 year at room temperature storage.
• The formulation and processing of PR1-500A were designed with regard to occupationaland environmental safety. The principal solvent in PR1-500A is 1-methoxy-2-propanol anddevelopment of PR1-500A is accomplished in a basic water solution.
Properties
♦ Solids content (%) 11-15
♦ Principal solvent 1-methoxy-2-propanol
♦ Appearance red yellow liquid
♦ Coating characteristic very uniform,striation free
♦ Film thickness after 100°C oven bake for 15 minutes
Coating spin speed, 40 s spin (rpm): (nm)
1000 720-8202000 570-6703000 450-5504000 310-4105000 270-370
♦ Sensitivity (mJ/cm² for 1 μm thick film):365 nm exposure wavelength 70436 nm exposure wavelength 40
♦ Guaranteed shelf life at 25°C storage (years) 1
Processing
1. Application of resist by spin coating at selected spin speed for 40 s.
2. 120°C hotplate bake for 120 s or 100°C oven bake for 20 minutes.
3. Resist exposure in a tool incorporating 365 or 436 nm wavelength.
4. Develop the resist by immersion with agitation or by spraying with aqueous Resist
Developer RD6 at a constant temperature in the 20-25 °C range until the exposed resist is
developed away. Allow an additional 4 seconds for overdevelopment.
Development time for 0.5 μm thick film in RD6 is 8 s.
Development time for 0.5 μm thick film in RD6/water 3:1 is 20 s.
5. Resist rinse in deionized water until water resistivity reaches prescribed limit.
6. Drying of resist.
7. Removal of resist in Resist Remover RR4 or in acetone.
Note: The above procedure refers to substrates, which are good conductors of heat such as silicon, GaAs etc. Bake times need to be increased 3.5 times for substrates, which are poor conductors of heat such as glass.